Posts about History
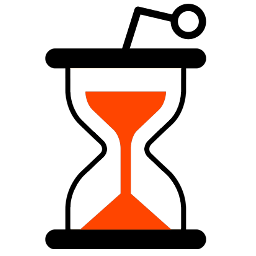

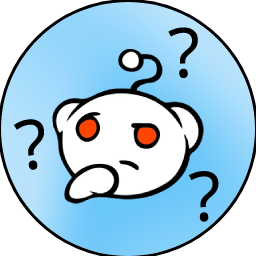
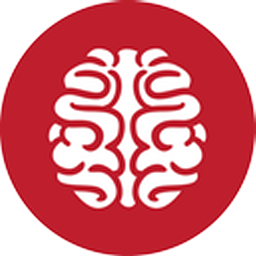





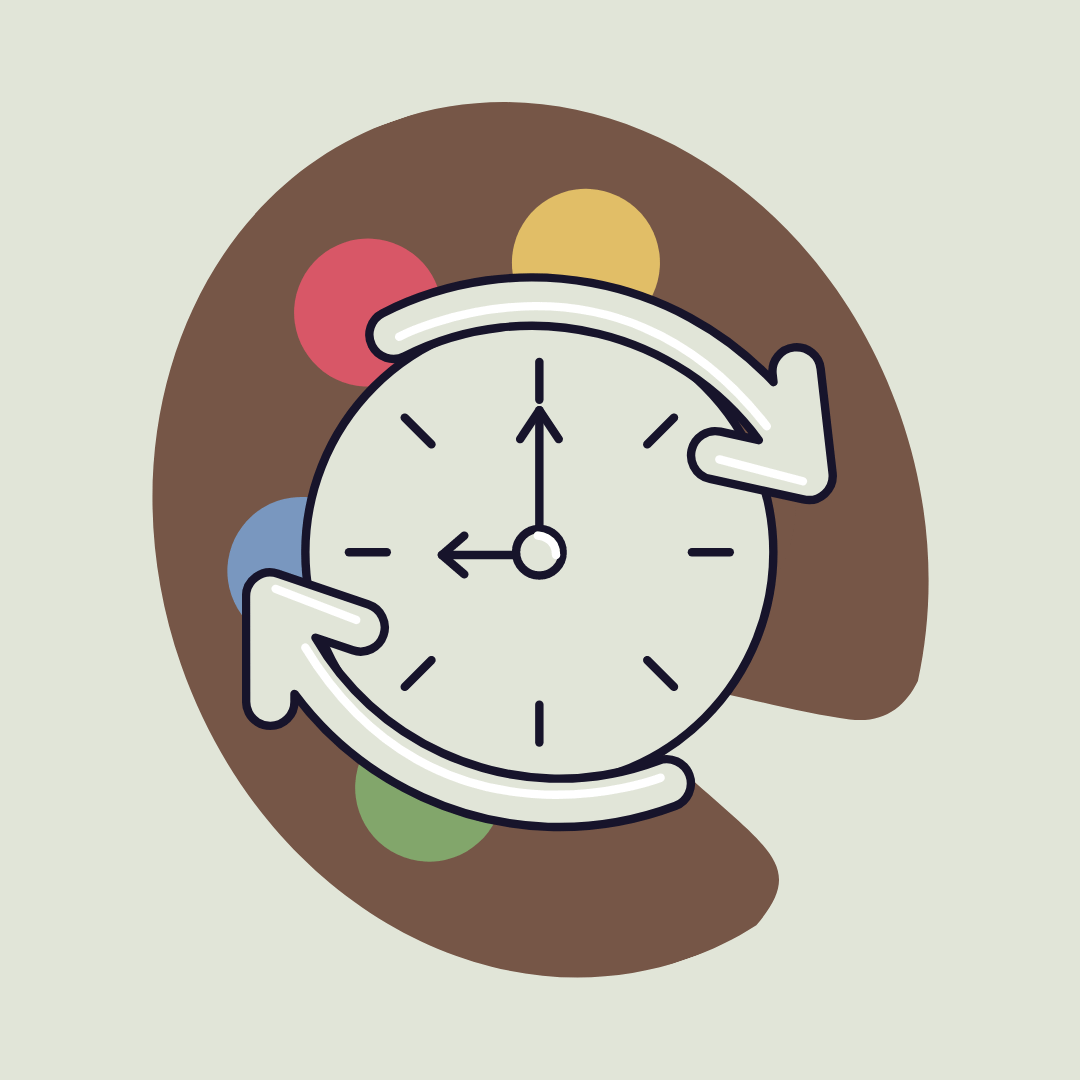
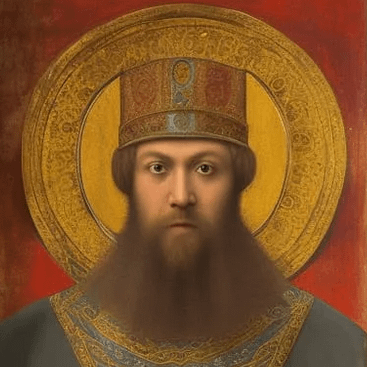
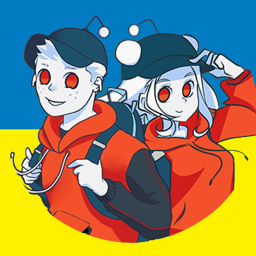

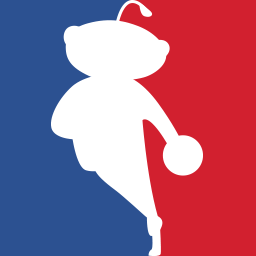

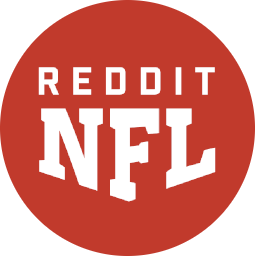








Because it has come up repeatedly over the last week on subreddits I moderate, I thought I'd revise and repost this quick explainer on the very prolific myth that "true" damascus steel is a lost art.
First of all, let's clarify what I mean when I say "True Damascus Steel", because it is very easy to become mired in definitions and ambiguity.
Top: Ottoman Pala, Pattern welded. Bottom, Iranian Shamshir, Crucible steel.
"Damascus steel" usually refers to two main types of steel:
The most common you'll see made today is "pattern-welded steel", where alternating layers of nickel rich and nickel deplete steel are stacked, forge welded, and folded or manipulated to create a pattern. The blade is then polished and etched to reveal the layers. While modern pattern welded blades typically use nickel containing steels to maximise contrast, historically this was not the case.
This method of construction using stacked, folded or otherwise forge welded, dissimilar* steels is how the majority of sword steels were made, worldwide, until advances in technology allowed for the use of more homogenous steel products. Pattern welding, and variants such as multibar patterns and laminated blades, were used widely and includes swords like spatha, โvikingโ swords, katana and more. It is worth noting that even "monosteel" swords which were made without the use of dissimilar steel, but still made from bloomery or refined blast furnace steel, were also subject to similar stacking, folding and forge welding techniques.
*Bloom is here considered to contain multiple dissimilar steels due to the heterogeneous nature of bloom.
This description of pattern welding and forge consolidated steels is intentionally simplified as they are not the focus of todays post, however for more information - particularly on bloomery and blast furnace production of steels - I recommend "The Knight and the Blast Furnace" by Alan Williams.
In the present day, this is the type you will see chefโs knives, swords, and even pocket knives being made of, and it can range from being rather cheap to incredibly expensive depending on the materials and workmanship.
Pattern welded Pala blade in \"Turkish Ribbon Twist\" style.
The other type of "Damascus Steel" is a form of hypereutectoid, pattern forming crucible steel.
And that is what I will be discussing today.
It is a hypereutectoid steel, which means that it has over 0.8% carbon by definition. It is formed by liquifying steel in a crucible, and is NOT produced by folding or layering steel. The typical composition is around 1% to 2% carbon, which by modern standards makes this an โultra-high carbon steelโ, often abbreviated as UHCS.
It is formed by melting steel with specific impurities in a crucible (historically, made of high kaolin content clay, rice husks as chaff, quartz sands, and other additives), and the process of turning this crucible โchargeโ into steel is quite complicated, with the potential for failure to produce an attractive pattern being high if any part of the process is not conducted correctly.
In summary, the crucible charge is brought up to melting temperature, and held at this temperature for a while, allowing the constituent alloying elements present in the steel to spread and bubbles to boil out. It is then slowly cooled, before the ingot is removed, roasted to decarburise the rim, drawn out into a bar, manipulated to produce a surface pattern with ball peens, wedges and grinding, and finally forged it into a blade, and thermally cycled.
As stated, this steel is typically the range of carbon content is between 1 and 2% in historical examples, and thus melts in a temperature range between 1200 and 1400c (for more information, see โiron carbon phase diagramsโ). It must also have sufficient levels of carbide formers (vanadium, molybdenum, manganese etc) in order to form patterns (Verhoeven et al, 1998,. Verhoeven et al 2018).
The pattern in crucible steel are formed by "rafts" of steel rich in carbide formers, where ultra-hard cementite spheroids form over subsequent forging cycles, which etch bright, and areas devoid of carbide forming elements (CFEs), which remain as pearlite, a soft mix of carbides which etches dark. The shape and size of the rafts is determined by the length of dendrites that form during the slow cooling of the ingot, as dendritic regions of the steel are carbide former depleted, and interdendritic regions are carbide former rich (Verhoeven et al, 2018).
Crucible steel shamshir blade, kara Khorasan pulad
Many people conflate pattern-welded steel with crucible steel, and call both โDamascusโ. Whilst this is accepted in colloquial language, it is important to distinguish between the two โ particularly when it comes to identifying antiques, or documenting them.
"Damascus" can therefore be used to refer to either pattern welded, or crucible steels, as both are pattern-forming steels, but it is best to specify which sort of "Damascus" is being discussed. The term has been used historically to describe both pattern-welded steel and crucible steel. Many swords and gun barrels made in germany were marked "damastahl" in the 18th and 19th century, and they were pattern welded, so there is historical precedent for such a naming convention, but the two techniques (and end products) are very different.
To be ABSOLUTELY CLEAR: "True" damascus steel is herein used as a term to refer to historical, patterned crucible steel. I am using this term entirely because it is understandable. The correct naming and etymology is discussed later. Both pattern welded and crucible steel blades can be called "damascus", and were historically, but the "lost" form is the crucible steel form.
The Myth: "Damascus Steel is a Lost Art":
The is quite a long history of crucible โDamascusโ steel, in the form of primary sources in which the process was written down - as early as 350BCE - 420BCE Zosimus, an early alchemist in Alexandria, wrote the following:
"The tempering of Indian Iron: Take 4 pounds of soft iron, and the skins of myrobalans, called elileg, 15 parts; belileg, 4 parts; and two parts of glassmakers magnesia. Then place it into a crucible and make it level. .... Put on the charcoal and blow the fire until the iron becomes molten and the ingredients become united with it. ... Such is the premier and royal operation, which is practiced today and by means of which they make marvelous swords. It was discovered by the Indians and exploited by the Persians".
This is by no means the only method to make crucible steel - some was co-fusion, using both cast iron and bloom, while some was indeed made with bloomery and carbon bearing material (often plants).
Incidentally, the oldest known crucible steel sword is from the 6th to 3rd century BCE and was found interred in a megalithic site in Thelunganur, Tamil Nadu, India (Ramesh et al, 2019) and daggers from ~500BCE have been found with the associated production site in Kodumanal, Tamil Nadu (Sasisekaran & Rao, 1999. Sasisekaran, 2002). This is consistent with the Zosimus account describing the technique as discovered by India.
Thelunganur sword, Ramesh et al 2019
The Islamic writers al-Kindi (full name Abu Ya'qub ibn Ishaq al-Kindi - circa 800CE - 873CE) and al-Beruni (full name Abu al-Rayhan Muhammad ibn Ahmad al-Biruni - circa 973CE - 1048CE) both wrote detailed procedures for the production of crucible steel, too.
โ?This is how Biruni described it in the manuscript Al-Jamรขhir Marefat al-Jawรขher. (From Khorasani et al, 2013):
โHe says that they [ironwokers] include five ratl ุฑุทู of [horse] shoes, the nails of which are made of narmรขhan ูุฑู ุขูู] in the crucible]. Then they add ten derham ุฏุฑูู of each [of the ingredients] rusaxtaj ุฑูุณุฎุชุฌ] antimony], marqiลกa-ye talรขโi ุทูุงุฆู ู ุฑููุดุง] golden marcasite] and meqnesiyรข ู ุบูุณูุง] meqnisiyรข ู ุบููุณูุง ;manganese dioxide MnO2] to the crucible, close the crucible with clay, and put it in the furnace. Then they fill the furnace with charcoal and blow air with Rumi (Roman Byzantine/Anatolian) bellows that are pumped by two men until the iron melts. Then they add a combination of halile ููููู) myrobalan), pust-e anรขr ุงูุงุฑ ูพูุณุช) pomegranate peel), melh al-ajeyn ู ูุญุงูุนุฌูู) the salt used for dough), and sadaf-e morvarid ู ุฑูุงุฑูุฏ ุตุฏู) pearl shell). From each the same amount approaching forty derham ุฏุฑูู are placed into small bags. One small bag is then added to each crucible. They keep heating vigorously without pause for one hour and then stop the heat. After it cools off, they take out the iron ingot (egg) from the crucibles. A person said that he was sitting next to a smith who was making swords in the province of Send ุณูุฏ] Sind]. He saw that the smith was using narmรขhan ูุฑู ุขูู and putting a very soft, ground mixture, which had a red color on it. Then the smith placed it in the furnace, and took it out and hammered it, and continued this process a couple of times. When asked why he did that he looked contemptuously. When he [the person sitting next to the smith] looked closely, he saw that the smith was hammering and mixing dus ุฏูุต with narmรขhan ูุฑู ุขูู the same way they made iron ingots (eggs) in Herat.โ
The metallurgical research into how this steel gets its patterns spans back far, with Michael Faraday (yes, that Faraday) having published a paper on recreating Indian crucible steel (known to him as wootz) in 1819, with subsequent papers in 1820 and 1822. It wasn't until 1837 when Pavel Anasov, a Russian metallurgist and director of the Zlatoust arms factory, that it was successfully recreated in any substantial quantity. Since then, research has been done on modern steels (Sherby and Wadsworth, 1983) and on historical blades, revealing the mechanisms by which the patterns forms (Verhoeven et al, 1998).
Anosov was a metallurgist and Colonel of the Russian Army during the occupation on the Emirate of Bukhara in the 1820โs, when he established contact with steelmakers in the region and attempted to recreate the steel in his steelworks in Zlatoust, but after failing asked Captain Massalski (results published 1841) whose regiment was stationed there, to observe the process and undertake further observations.
Massalski documented the Bukhara method, noting 3 key metals, cast iron, iron, and silver. Massalski stresses the ratio of one part iron, 3 parts cast iron (N.B: a co-fusion method of making steel with the right amount of carbon) and the crucibles hold around 2.5kg of steel, making up 1/3rd of the potential capacity of the crucible.
The metal workers start the fire and the metal begins to melt after some 5 to 6 hours, and makes a bubbling sound. When the bubbling sound ends, this is a sign that the fusion has ended. The workers remove the lid, add 0.013kg to 0.017kg of silver, stir rapidly with an iron rod, cover the charge with charcoal, and cover again with the lid. (N.B: this was a potentially primitive form of "killing" the steel, a process by which reactive elements in the charge react with another reactive metal - silver in this case, aluminium in modern times - and are thus removed from the reaction, resulting in less porosity due to gas production. The other method of degassing historically used was simply holding the ingot at the molten, liquidus temperature for longer).
N.B: Silver is not particularly reactive, so the purpose of silver might not have been killing the steel. The atmosphere and composition of a crucible melt, as well as the 1400-1500c temperature at which silver was added require further investigation to determine the mode of action. it may be that the liquid silver was moving into the grain boundaries of the steel during solidification, displacing phosphorus or sulphur.
They return the crucible to the fire and allow it to cool as the charcoal burns out, slowly, over 3 days. After cooling, the ingot is removed and tested by polishing to check for dendrites. The steel then passes to smiths, who โknow that from then onwards whether the ingot survives being forged is a matter of luckโ
A freshly made crucible steel ingot, image credit Peter Burt
This is clear evidence that not only was the crucible steel production process being conducted in Bukhara in 1841, but that the mechanisms of pattern formation were already being formally investigated. And this is by far not the most recent ethnographic account of crucible steel manufacture.
In Mawalgaha, Sri Lanka, Ananda Coomaraswamy documented crucible steel production in 1903 โ (Coomaraswamy, A. (1908): Medieval Sinhalese Art. Pantheon Books, New York, Juleff et al 2009). He found two crucible ingot fragments, crucibles, iron blooms and small iron bars. The two crucible ingot fragments were collected from the Mawalgaha village, where Kiri Ukkuwa demonstrated how to make steel for Coomaraswamy โ providing the most recent known eyewitness evidence for crucible steel manufacturing.
This form of "Damascus" steel was therefore historically used as early as the 6th century BCE (Park et al 2019) and as late as 1841 when Massalski recorded crucible steel production in Bukhara, leading to the production of Bulat in Zlatoust by Anosov, and 1903 in Sri Lanka (though it was not actively being made en masse, and was only demonstrated using previously abandoned equipment).
In summary: Production between 1903ish, and 1980ish, was virtually halted, thus leading to the myth of it being a "lost art", however as will be shown in this document, the process was well documented and has since been replicated.
The result is that there are now upwards of 150 individuals (at least, that I know of) who can produce crucible steel with an accurate metallurgical composition, which naturally form patterns in the steel due to carbide segregation. It is structurally, functionally and visually identical to historical crucible steel - and can only be differentiated by analysing the amount of radionuclides in the steel, as all historical steel is low background steel, and modern recreations are typically not.
Because I recognise that metallurgy is easier to grasp with visual aides, here is a comparison of antique crucible steel from an Iranian shamshir in my collection, and modern crucible steel (made by Niko Hynninen).
Crucible steel (modern) by Niko Hynninen.
Etymological information on "Damascus" steel:
Utsa / Wootz (Sanskrit- and mistranslated Sanskrit), Urukku (Tamil) Pulad (Persian), Fuladh (Arabic), Bulat (Russian), Polat (Turkish) and Bintie (Chinese) are all names for ultra-high carbon crucible steel typified by carbide segregation, which can be otherwise referred to as "crucible damascus steel". The modern term โwootzโ first appears around 1794 in writings by Sir Joseph Banks, who mistranslated Sanskrit for โutsaโ as โwootzโ (Dube, 2014). In the regions where crucible steel was made, and where it was forged into blades, it was not called "damascus". This name is primarily a medieval name, and primarily used in Europe.
The origin of the name "Damascus" steel is contentious - The Islamic writers al-Kindi (full name Abu Ya'qub ibn Ishaq al-Kindi) (circa 800 AD - 873 AD) and al-Beruni (full name Abu al-Rayhan Muhammad ibn Ahmad al-Biruni) (circa 973 AD - 1048 AD) were both scholars who wrote about swords and steel made for swords, based on their surface appearance, geographical location of production or forging, or the name of the smith.
There are three potential sources for the term "Damascus" in the context of steel.
The word "Damas" stems from the root word for "water" ("ma") or "broiling" in Arabic (Sachse, 1994, 13) and Damascus blades are often described as exhibiting a water-pattern on their surface, and are referred to as "watered steel" not only in English but in other languages.
The second theory is geographical, as Al-Kindi called swords produced and forged in Damascus as Damascene (al-Hassan, 1978, 35) but it's worth noting that crucibl steel blades were made in many nations, and crucible steel is not known to have ever been produced in the city of Damascus. Al Kindi also describes crucible steel production using the typical term Pulad, distinct from these damascene swords, indicating that the two types are separate. It is also worth noting that Al-Kindi did not describe these swords as having pattern forming steel.
Third, Beiruni mentions a sword-smith called Damasqui who made swords of crucible steel (Said, 1989, 219-220). In a similar fashion, Al-Kindi mentions swords called โZaydiya which were forged by a man called Zayd, and hence they were attributed to his name". We therefore have a precedent for naming swords based on their makers, which may explain how "Damascus" came about.
It is my opinion that the "watered" hypothesis is most likely for the origin, though the popularisation of the term may have indeed occurred due to western travellers who purchased the swords in damascus, and described them thusly, as it was a massive center for trade.
How Crucible steel gets its pattern:
Crucible steel, as the name implies, is made in a crucible process, and requires completely liquefication of the crucible charge.
Most surviving "recipes" for crucible steel call for either a combination of bloomery iron, and cast iron, or the use of bloomery iron and organic carbon sources (like plant leaves) - but crucible steel recipes included other elements, like organic material - rice husks, leaves, bark - as well as shells, glass, and even silver. The trace impurities in the iron used, and in these additives, are key to the patterns they show after forging.
In order to form patterns, carbide forming alloying elements like vanadium, tungsten or manganese are necessary in small amounts, with vanadium being the most common historical alloying element. These carbide formers cause the segregation of hard cementite carbides, which form the "white streaks" in crucible steel.
The segregation of CFEs into interdendritic reasons is due to the differences in solidification temperature between high CFE and low CFE steel, with low CFE steel solidifying at a higher temperature than high CFE steel. This causes the low CFE steel to solidify first when the ingot is slowly cooled, and it does so by branching out into dendrities of relatively pure iron, while the impurities such as phosphorus, CFEs and sulfur get pushed into the regions between these branches.
Dendritic structures visible on freshly made crucible ingot - image credit Peter Burt.
During the forging of the crucible steel "puck", these carbide formers are pushed into parallel, layered sheets in the microstructure of the steel (Verhoeven et al, 1998).
Because vanadium and other CFEs do not readily dissolve at forging temperatures and do not rapidly migrate at forging temperatures, these sheets of carbide formers form distinct bands in the steel. As the steel is thermally cycled, carbides aggregate onto the CFEs via ostwald ripening, and form spheroids of cementite. The interdendritic regions without CFEs form as pearlite, a soft two-phase mixture of carbides, or sorbite, and imperfect form of pearlite. This is diagnostic of historical crucible steel (Verhoeven et al 2018, Feuerbach 2002, Feuerbach 2006).
It is worth noting that vanadium is not the only effective carbide former found in historical crucible steel blades, and other carbide formers like manganese are seen in historical examples - or even chromium as seen in Chahak, Iran (Alipour et al 2021). Additionally, the other microalloying elements in the steel can effect the contrast and spacing of the pattern, with phosporus notably increasing the contrast of the pattern after etching (Khorasani and Hynninen, 2013)
Historical perspectives on Crucible Damascus Steel quality:
Regarding the historical reputation of historical crucible steel swords: they were always very expensive, very desirable, and very well thought of - HOWEVER - there are accounts from the 14th century of cold-short blades (high in phosphorus) which claims that crucible steel swords are prone to breakage in cold weather.
The exact quote is by Aliฬ ibn สปAbd al-Rahฬฃmaฬn Ibn Hudhayl, translated:
"the Hindy sabre often breaks when the weather is cold and shows itself better when the weather is warmโ
Despite this, they were very valued. Mohammad ibn Abi al-Barakฤt Jลhari Nezฤmi in 1196 CE states a good shamshir blade of crucible steel was valued at 100 golden Dinar (Khorasani et al, 2013).
Al-Idrisi (Full name Abu Abd Allah Muhammad ibn Muhammad ibn Abd Allah ibn Idris al-Idrisi - circa 1100CE - 1166CE) claimed that "nothing could surpass" the edge of a crucible steel sword.
Bertrandon de la Brocquiere, a Frenchman, wrote about his travels to the Middle East in 1432CEโ1433CE. He wrote:
"Damascus blades are the handsomest and best of all Syria... I have nowhere seen swords cut so excellently. They are made at Damascus, and in the adjoining country."
Note: This is potentially the source of the (incorrect but often repeated) claim that crucible steel swords were made in Damascus.
In the early 1600's, Polish king Zygmunt III Waza ordered a Armenian merchant (Sefer Muratowicz) to purchase a number of watered steel blades from Isfahan, Persia due to their value and reputation (Muratovich et al, 1777). On this same journey, the merchant purchased carpets embroidered with the royal coat of arms, which still survive today.
Regardless of the reputation crucible steel enjoyed in its' day, the reality is that it was by nature very clean, with minimal slag - which made it less likely to break due to inclusions - and there is a lot of variation in the metallurgical composition of this steel. Some have higher carbon, or more phosphorus, and the quality varied. Heat treatment also widely varied.
Compared to bloomery steel which was folded and consolidated, it's more uniform and much lower in slag - the term for non-metallic inclusions. The same is true of refined blast furnace steel, which also requires forge consolidation after finishing the finery process.
Crucible steel can be more brittle, depending on the heat treatment, phosphorus, and sulfur contents, or it can be much more flexible. It depends on the exact sword being analysed, as crucible steel was produced for around 2 millennia and in many places. For example, some accounts of crucible steel swords being able to be bent 90 degrees exist, however these can easily be countered with extant examples that take a set no matter the degree of bending.
Production methods:
Here are 4 different processes, which were recorded from at early as Al Kindi, to as late as 1841CE with Massalski - from the Deccani process used in Hyderabad, to the south Indian process, and the Isfahan process, and the Bukhara process.
There are more processes out there, I just haven't gotten around to writing them out.
Bukhara:
3 parts clean iron, 1 part cast iron. Place in a crucible that is five times as tall as it the base is wide, with a mouth three times the size of the base. The weight of iron should be 2-2.5kg.
Using a charcoal melting furnace with air venting holes, heat until melted (6 hours) or until a bubbling sound can be heard from the crucible. once bubbling stops, remove the lid of the crucible and add 0.013-0.017 grams of silver to the crucible and stir with a metal rod. reseal the crucible, seal all holes in the furnace, and allow to cool over 3 days.
Remove the puck from the crucible, and polish one corner of it to check if the watered pattern is good. If the pattern is poor, reheat to a red heat and hold for seven minutes before allowing to cool in air.
Forge into a bar using the top of the button to form the spine of the blade, and never heating above red.
South Indian:
In a clay crucible of conical form (200mm height x 50mm diameter) add 250-500 grams of bloomery iron, as well as wood chips, rice husks, vines or leaves. Seal the crucible with a clay lid, leaving a vent hole. Allow to fully dry
Using a bellow-fed charcoal forge, heat for 6 hours or until molten. allow the crucible to cool in the forge (some sources say to quench it in water).
The button will have a striated appearance if everything was done correctly.
Deccani (Hyderabad) Process:
Using a mixture of iron sand derived iron ore, and iron clay derived iron (mirtpalli and kondapur iron), place in a crucible with glass, sealed with clay with a vent hole. Place in a bellow powered charcoal furnace for 24 hours. The steel will melt within the first 3. After 24 hours, remove crucible and allow to cool in the air.
Once cool, remove the buttons and cover each in clay, and anneal in a conventional forge for 12-16 hours. repeat this annealing process until the button is no longer brittle.
Isfahan Process:
To a crucible, add 10% casi auriculata wood, and asclepias gigantean leaves with two parts pure iron, one part cast iron, and three parts silicate-rich iron ore up to a total weight of 200 grams.
10-1200 of these small crucibles are heated at a time in a kiln operated with charcoal and bellows for 6 days, before the crucibles are broken open, and the buttons removed.
The buttons are then transferred into a "hot room" to anneal and temper for 2 days so they do not shatter from cooling too quickly.
Authors note: I suspect that if this room is a furnace-heated compartment, and is hot enough, they also experience some level of rim decarburisation, as well as converting the microstructure of the puck to a more forgeable state compared to steel which has not been roasted.
**References**
Alipour, R., Rehren, T., Martinรณn-Torres, M. "Chromium crucible steel was first made in Persia", Journal of Archaeological Science, Vol. 127, 2021,
Al-Hassan, A.Y., 1978, Iron and Steel Technology in Medieval Arabic Sources, Journal for the History of Arabic Science 2: 1,31-43
Anosov, P.P. (1841) On the Bulats (Damascus Steels). Mining Journal, 2, 157-317.
Dube, R.K. (2014) Wootz: Erroneous Transliteration of Sanskrit โUtsaโ used for Indian Crucible Steel. JOM 66, 2390โ2396
Feuerbach, A. M. 2002. Crucible steel in Central Asia: production, use and origins.
Feuerbach, A. M. 2006. Crucible damascus steel: A fascination for almost 2,000 years. JOM, 58, 48-50.
Juleff, G. Craddock, P.T., Malim, T. (2009) 'In the footsteps of Ananda Coomaraswamy: Veralugasmankada and the archaeology and oral history of traditional iron smelting in Sri Lanka', Historical Metallurgy: The Journal of the Historical Metallurgy Societyย?vol. 43(2) pp. 109-134
Khorasani, Manouchehr & Hynninen, Niko. (2013). Reproducing crucible steel: A practical guide and a comparative analysis to persian manuscripts. Gladius. 33. 157-192. 10.3989/gladius.2013.0007.
Muratowicz, S., Minasowicz, J.E., Mitzler de Kolof, M. (1777) Relacya Sefera Muratowicza Obywatela Warszawskiego Od Zygmunta III Krola Polskiego Dla Sprawowania Rzeczy Wysลanego do Persyi w Roku 1602. Warsaw, published by J. K. Mci y Rzpltey Mitzlerowskiey, .
Park, J.โS., Rajan, K., and Ramesh, R. (2020) Highโcarbon steel and ancient swordโmaking as observed in a doubleโedged sword from an Iron Age megalithic burial in Tamil Nadu, India. Archaeometry, 62: 68โ 80.
Sachse, Damascus Steel: Myth, History, Technology, Applications (Wirtschaftseverk: N.W. Verl. Fur Neue Wiss, 1994).
Said, Al-Beruni's Book on Mineralogy: The Book Most Comprehensive in Knowledge on Precious Stones (Islamabad: Pakistan Hijra Council, 1989), pp. 219โ220.
T., F. Metallurgical Researches of Michael Faraday. Nature 129, 45โ47 (1932).
Verhoeven, J., A.H. Pendray, WE. Dauksch, 1998, The Key Role of Impurities in Ancient Damascus Steel Blades, JOM 50:9, 58-64
J.D Verhoeven, A.H Pendray, W.E. Dauksch, 2018, Damascus steel revisited, JOM vol 70, pp 1331-1336
Oleg D. Sherby: "Damascus Steel Rediscovered?" 1979, Trans. ISIJ, 19(7) p. 381--390.
J. Wadsworth and OD. Sherby, 1980 โOn the Bulat - Damascus Steels Revisitedโ, Progress in Materials Science. 25 p. 35 - 68
Sherby , O.D. and Wadsworth, J., 1983-84 "Damascus Steels --- Myths, Magic and Metallurgy", The Stanford Engineer, p. 27 - 37.
J. Wadsworth and O.D. Sherby, "Damascus Steel Making", 1983, Science , 216, p. 328-330. 1985
Oleg D. Sherby, T. Oyama, Kum D. M., B. Walser, and J. Wadsworth, 1985, "Ultrahigh Carbon Steels". J. Metals, 37(6) p. 50 - 56.
Oleg D. Sherby and Jeffrey Wadsworth, 1985, "Damascus Steel", Scientific American, 252(2) p. 112 -120
N.B: A brief note on the claim carbon nanotubes exist in crucible steel:
The only articles that "found" carbon nanotubes was published as a brief communication to Nature, i.e not a full article. This was in 2006, and was only a few pages in length.
It later found its away into a conference paper by the same authors, still not a full length peer reviewed research article. This was 2 pages in length. These findings should be considered preliminary.
The method used (dissolving crucible steel in acid and seeing what remains) revealed stands of carbon, but carbon dissolves VERY readily into steel. Crucible steel is typified by cementite spheroids, which often stretch into rods during forging as they are deformed. If you dissolve cementite in acid, removing the iron component, you are left with carbon.
This does not mean there was an intact carbon nanotube in the core of the cementite rod - and even if it DID mean that, it would have negligible impact on performance because it is *encased* in cementite, which itself is in a soft matrix of pearlite or sorbite.
But don't take my word for it. Other academics, including those who have been instrumental in understanding crucible steel (namely John Verhoeven) doubt the findings.
" John Verhoeven, of Iowa State University in Ames, suggests Paufler is seeing something else. Cementite can itself exist as rods, he notes, so there might not be any carbon nanotubes in the rod-like structure."
"Another potential problem is that TEM equipment sometimes contains nanotubes, says physicist Alex Zettl of the University of California"
https://www.nature.com/news/2006/061113/full/news061113-11.html